What Are the Challenges of CNC Milling Brass and Copper Parts?
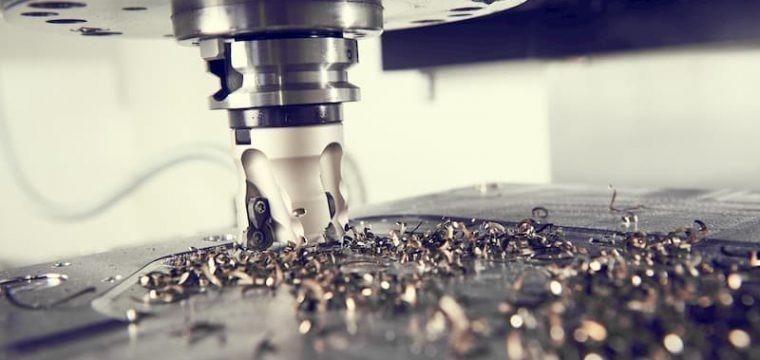
CNC milling has many benefits when it comes to machining brass and copper parts, but there are certain challenges as well that must be carefully considered to guarantee successful production. Here are some of the key challenges associated with CNC milling brass and copper:
l Softness and Ductility: The comparatively soft and ductile nature of copper and brass can present several machining difficulties. Especially during high-speed cutting operations, their softness renders them vulnerable to deformation and burr formation. Furthermore, gummy buildup from their ductility may occur on cutting tools, further compromising tool life and surface finish.
l Heat Generation and Thermal Conductivity: Since copper and brass are good heat conductors, heat may be produced during the machining process. This heat generation can have an impact on material properties and dimensional accuracy by causing tool wear, thermal expansion of the workpiece, and possible annealing of the material.
l Chip Control and Entanglement: Controlling chips during the machining process can be challenging due to the soft and ductile nature of copper and brass. Long, stringy chips have the potential to entangle in the cutting tool and workpiece, causing chatter, vibration, and even damage.
l Surface Finish and Tool Wear: The tendency of brass and copper to deform and produce burrs makes it difficult to achieve a smooth and consistent surface finish on these parts. Furthermore, high feed rates or cutting speeds can accelerate tool wear due to these materials' softness.
l Tool Selection and Material Compatibility: Selecting the appropriate cutting tool material and geometry is essential for maximizing the efficiency of the CNC milling process for copper and brass. Because of their hardness and resistance to wear, carbide tools are typically chosen; however, the geometry and coating of the tool must be customized to the particular material and machining parameters.
l Fixturing and Workpiece Stability: When CNC milling brass and copper parts, proper fixturing and workpiece stability are crucial for maintaining dimensional accuracy and minimizing vibration. These materials' ductility and softness make them more prone to chatter and deformation if improperly clamped.
l Coolant Selection and Application: To avoid heat generation and thermal effects when CNC milling copper and brass, effective cooling is essential. The particular material, the cutting parameters, and the machine tool's capabilities determine the kind and rate of coolant.
l Post-Processing and Finishing: The functional properties, dimensional tolerances, and surface finish of CNC milling brass and copper parts may require post-processing or finishing operations, contingent on the particular application and its requirements.
Manufacturers may optimize the CNC milling process for brass and copper parts by comprehending and resolving these issues, guaranteeing the creation of premium parts with consistent dimensions, smooth surface finishes, and required material properties.
- Art
- Causes
- Crafts
- Dance
- Drinks
- Film
- Fitness
- Food
- Games
- Gardening
- Health
- Home
- Literature
- Music
- Networking
- Other
- Party
- Religion
- Shopping
- Sports
- Theater
- Wellness