Energy Efficiency in Extrusion Compounding Machines: A Deep Dive into Power Consumption
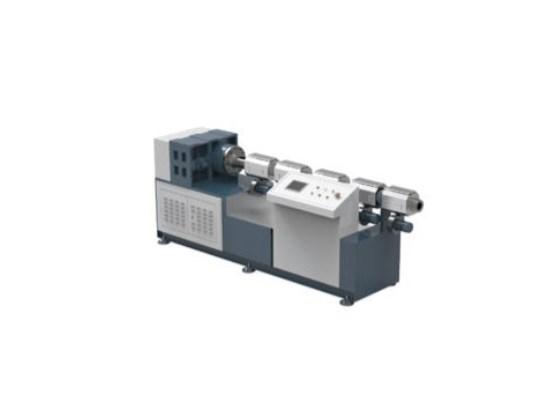
The energy consumption of the Extrusion Compounding Machine is a significant concern for manufacturers in the plastics and rubber industries. These machines are workhorses, responsible for the continuous mixing and compounding of raw materials to produce a uniform melt that can be shaped into various products. The efficiency of an Extrusion Compounding Machine not only affects the bottom line but also has implications for environmental sustainability.
In the quest for more sustainable manufacturing practices, the focus on reducing the energy consumption of Extrusion Compounding Machines has become increasingly important. These machines, which are central to the extrusion process, consume a considerable amount of energy, primarily due to the high temperatures and pressures required for the compounding process. The energy used in an Extrusion Compounding Machine can be broken down into several components, including motor drives, heating elements, and cooling systems.
The motor drives of Extrusion Compounding Machines are responsible for a significant portion of the energy consumption. These motors power the screws that push the material through the machine, and their efficiency can be improved through the use of variable frequency drives (VFDs). VFDs allow for precise control of the motor speed, which can reduce energy consumption by matching the motor output to the process demand.
Heating elements in Extrusion Compounding Machines are another significant contributor to energy use. These elements are necessary to raise the temperature of the material to the point where it can be effectively mixed and compounded. However, the efficiency of these heating elements can be improved through the use of high-efficiency burners, better insulation, and heat recovery systems. By capturing and reusing waste heat, manufacturers can reduce the amount of energy required to maintain the necessary process temperatures.
Cooling systems in Extrusion Compounding Machines are also energy-intensive, as they are responsible for removing excess heat from the process to maintain optimal operating conditions. The efficiency of these cooling systems can be improved through the use of more efficient heat exchangers and by optimizing the cooling water flow rates.
In addition to these direct energy consumption components, there are also indirect factors that can influence the energy consumption of Extrusion Compounding Machines. For example, the design of the machine itself can have a significant impact on energy use. Machines with a more efficient screw design can process materials with less energy input, while machines with better insulation can reduce heat loss and improve overall energy efficiency.
Maintenance and operational practices also play a role in the energy consumption of Extrusion Compounding Machines. Regular maintenance can ensure that the machine is operating at peak efficiency, while proper operational practices can help to minimize energy waste. For instance, using the correct material formulations and processing conditions can reduce the energy required to achieve the desired product quality.
In conclusion, the energy consumption of Extrusion Compounding Machines is a complex issue that involves a variety of factors. By focusing on improving the efficiency of motor drives, heating elements, and cooling systems, as well as optimizing machine design and operational practices, manufacturers can significantly reduce the energy consumption of their Extrusion Compounding Machines. This not only leads to cost savings but also contributes to a more sustainable manufacturing process, aligning with the growing global demand for energy-efficient and environmentally friendly production technologies.
https://www.extruderfactory.com/product/
- Art
- Causes
- Crafts
- Dance
- Drinks
- Film
- Fitness
- Food
- Games
- Gardening
- Health
- Home
- Literature
- Music
- Networking
- Other
- Party
- Religion
- Shopping
- Sports
- Theater
- Wellness